Fashion & upcycling
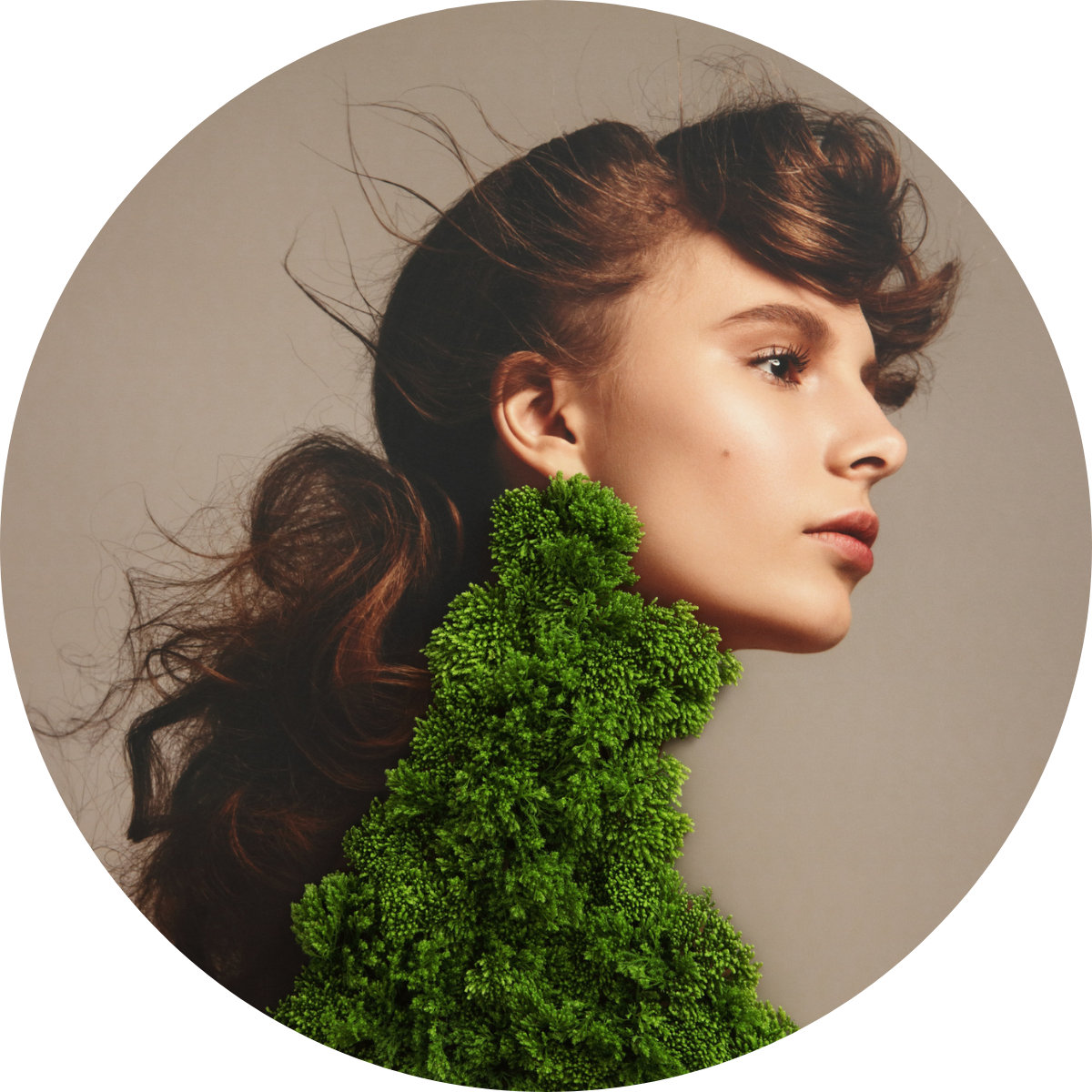
“How to reduce the Fashion impact on environment by producing fabrics from food waste and plants.”
Dressing up with love for the environment
The subtitle that I chose is the root of the article that I am about to tell you. I participated in fairs dedicated to the production of sustainable fabrics and a new world has opened to me. I realized how important is to combine the passion for fashion with the love for the environment.
Why do I tell you this, because we can no longer ignore the fact that fashion is one of the most polluting industries; in fact, it is estimated that about 10% of the damage caused to the environment derives from fashion. It is not a provocation by environmentalists, but reality.
Therefore, I do agree with the professionals of the sector that I am about to introduce you and who argue that innovation and love for the environment must necessarily be two missions on which to focus attention, not in the future, but immediately.
Today we can progress, develop, without causing damage to the environment. How? With technology and innovation that will help us be more sustainable.
However, not only consumers, but also fashion brands want more sustainable products, as the production of textile fibers has a heavy impact on the environment, and this is a positive challenge that many want to face.
Going deeper, what I want to present you are the avant-garde methods that the fashion industry has chosen to experiment to generate fabrics from food waste and plants; today it seems possible to “grow” clothes to save the environment and sustainable dressing.
In revealing you how all of this is possible, I am going to introduce some interesting Italian and international realities that have taken truly revolutionary steps with surprising results.
Salvatore Ferragamo:
Salvatore Ferragamo with his digital platform “Sustainable Thinking” has been connecting the sustainable projects and activities of the Maison for years to an international network of contributors with different experiences in the field. Furthermore, Sustainable Thinking, not just a digital project but also an exhibition of sustainable fashion works, at the Salvatore Ferragamo Museum in Florence.
Two of the companies that collaborated in “Sustainable Thinking “:
Orange Fiber:
One of the prominent projects, dating back to 2017 is the Ferragamo Orange Fiber Collection, the first fashion collection made with fabrics derived from citrus fruits, in collaboration with the Sicilian Company Orange Fiber. This extraordinary collaboration was born from the common interest in innovation, sustainability, and love for the environment.
The Ferragamo Orange Fiber Collection is a capsule embellished with prints by the Italian designer Mario Trimarchi that celebrates Mediterranean creativity, presented on the 47th Earth Day. This project represented Orange Fiber’s entry into the international market for sustainable fashion materials, even though it won the Global Change Award in 2015.
Let us find out the details whose Orange Fiber and what it does.
Orange Fiber is an all-Italian, Sicilian company that produces fabrics from orange peel and by-products of the citrus juice industry.
Not only citrus fruits are good to eat and drink, but also to dress, this is the revolutionary and visionary idea of the Sicilian Company and what derives from it is a refined fabric, of the highest quality, all from a precious resource and without subtracting raw material to the food industry.
In fact, every year in Italy, there are about 700,000 tons of waste from the citrus industry and this entails high costs for the environment; so why not find a way to reuse them with upcycling? Seeds, peels, leaves of citrus fruits are transformed to give life to a precious fabric such as silk. In practice, the citrus fruit waste is pounded until a cellulose is obtained for spinning. Today Orange Fiber is chosen by prestigious and luxury brands for the creation of extraordinary fabrics.
Ananas Anam:
Another interesting collaboration of Ferragamo was with Carmen Hijosa’s Ananas Anam, as well as creator of Piñatex, the eco-leather created with pineapple leaves, whose fiber is transformed with a chemical process.
Piñatex is an innovative, natural, and sustainable material, breathable, flexible and with a tensile strength comparable to that of linen and jute, hemp, and sisal. In addition, Carmen’s idea helps local growers earn more, as they can exploit the commercial value of pineapple leaves that would otherwise be thrown away.
In short, Orange Fiber and Ananas Anam are two of the different companies that have contributed to the supply of sustainable fabrics and materials for the exhibition at the Salvatore Ferragamo Museum in Florence, focused on alternative production processes, aimed at safeguarding our ecosystem.
Prada
Prada with the Prada Re-Nylon collection has started its commitment to upcycling. Re-Nylon is a fabric that can be regenerated several times, infinitely, without losing quality, a real “cyclic luxury”.
Basically, the Prada Re-Nylon is made entirely from a regenerated nylon created through the recycling and purification of plastic collected from oceans, fishing nets, landfills and textile fiber waste globally. Through a process of transformation into new polymers and then threads, this material can be recovered and transformed into new nylon fabric. The choice of ECONYL® yarn for the Prada Re-Nylon collection actively contributes to the reduction of global warming by up to 90% * compared to the use of virgin nylon yarn.
After creating the Prada Re-Nylon Collection, the brand has continued to commit itself to protecting the environment. Together with UNESCO, (more precisely together with the Intergovernmental Oceanographic Commission of UNESCO) it has created an education program for ocean sustainability, or “Sea beyond”. It is an educational program for secondary school students aimed at raising awareness of ocean conservation.
Lvmh, Fendi
There is recent news of Fendi’s desire to cultivate bio-fabrics for luxury in the laboratory and it will do so with the use of keratin, making use of the collaboration with the Imperial College of London and with Central Saint Martins to create innovative fibers. This project was born first of all to find alternatives to furs, which is why we talk about the use of keratin.
Biocouture:
Biocouture is the vegetable fashion of Sezanne Lee, an internationally renowned fashion designer, who aims to use nature to bring innovation to fashion. Basically, to create her collections, Suzanne makes use of biology, making materials with living organisms such as bacteria. Specifically, she starts from the cultivation of cellulose in the laboratory, to create clothes to wear. This technique is a combination of bio and nanotechnology, and the resulting products are therefore highly biodegradable. An example? To create an organic dress, you need green tea, sugar, some bacteria, and time. Fruits and vegetables are used for coloring, which can also make clothes antimicrobial. The problem is that this kind of cellulose is hydrophobic, since they are organic and therefore biodegradable, they decompose easily and this is Susanne’s next challenge together with her collaborators, to overcome the problem by studying new solutions and aiming at furnishing objects.
Desserto:
Another beautiful reality in the field of producing sustainable materials in fashion is Desserto, a company that creates vegan leather from cacti.
Desserto was born from the idea of Adrian and Marte, who after working in the furniture, automotive and fashion sectors noticed how serious the problem of pollution was becoming. They both wanted to produce something eco-sustainable, which was therefore not of animal origin. In fact, working and creating leather accessories and garments of animal origin means using a large amount of water and chemical agents that are usually toxic, so the products are not biodegradable.
Desserto is native to Mexico, a land rich in cacti, a very suitable plant for the production of leather that does not require a lot of water for processing. In addition, the cactus absorbs carbon dioxide, and this is highly positive for the environment.
It is important to say that to make cactus-derived leather products, only the ripe leaves are cut. The leaves are then washed, pounded, and the resulting mixture is left to dry for 3 days. The fabric obtained is totally biodegradable, flexible, breathable and lasts up to 10 years, sold at a cost that is equivalent to the product in leather of animal origin.
Thanks to this wonderful discovery, Desserto not only creates accessories for fashion, but also interior upholstery for cars, furniture items, with the aim of not only helping the environment but also creating new jobs.
Diana Sherer:
Diana Sherer is a German contemporary visual artist who, after years of studying the behavior of plant roots, has made them a working tool, creating fabrics for carpets, works and clothing thanks to the intertwining of roots.
In practice, the artist created a process of artificial growth of the roots that forces them to develop following decorative motifs, all with the collaboration of biologists from Radboud University in Nijmegen. The details of the production of these beautiful works remain a mystery, but what we know is that Diana has experimented with many types of seeds. Herbs and grains, especially oats, wheat and corn are her favorite varieties because they grow quickly, and their roots are strong.
For the Frankfurter Kunstverein, Diana Scherer created one of her great floor works, Interwoven, with which she allows oat seeds to grow into a fabric. Just a few hours before the exhibition opens, she reveals the plant tissue so that the bare roots are shown to visitors. Thanks to Interwoven, the artist won the New Material Award 2016.
Chiara Vigo:
Chiara from San’Antioco, in Sardinia, is the last woman to weave the “silk of the sea” and has been a candidate for Unesco intangible heritage since 2005. It is the byssus, a worked thread that derives from the keratin slime of the fin nobilis, a mollusk like the mussel but larger and anchored to the seabed. Once dried, the keratin produces a fine and precious filament, used in ancient times to make the dresses of Solomon and Nefertiti, or the gloves of the kings of Italy. For processing, the thread is passed through the pedal loom or worked with nails in small wooden looms. Chiara, however, is keen to clarify that it cannot be a salable material as it is not economically sustainable. On 100 dives you can get a maximum of 300 grams of raw, 30 grams of clean, which are 21 meters of wire. In addition, the “byssus” can also be colored in a vegetable or marine way, for example, with pomegranate juice, lemon seeds.
Chiara has made over seventy canvases and collaborates with the Faculty of Chemistry of Bologna and the Max Planck of Berlin, as well as the Department of Marine Biology of Cagliari and wants to continue to pass on her art.
What I have deduced from these extraordinary projects and ideas is that we have to look at things from a different perspective, because if we want to make things change, we have to change our vision.
Not only passion for fashion is enough to perform such great acts, but also an interest in the future; which is why I wholeheartedly consider the idea of totally using sustainable materials on my future collections.